Encoders
Speed measurement and position detection using incremental and absolute encoders.
Choose the perfect encoder for your application from a variety of sizes and ordering options. The Sendix encoder – made in Germany – is the result of the highest quality awareness and careful selection of materials. It has proved its value in many industries as a robust and precise sensor technology. Design your plants, machines, or motors with Kübler. Your application is our priority: Your modifications and special solutions are implemented flexibly and quickly. We look forward to your challenge.
Incremental and absolute
- Shaft and hollow shaft variants
- Size ranging from miniature Ø 24 mm to maxi Ø 100 mm
- Optical and magnetic sensing
- Wide operating temperature range and high protection class
- Standard, fieldbus, Industrial Ethernet interfaces
Encoders
Speed measurement and position detection using incremental and absolute encoders.
Choose the perfect encoder for your application from a variety of sizes and ordering options. The Sendix encoder – made in Germany – is the result of the highest quality awareness and careful selection of materials. It has proved its value in many industries as a robust and precise sensor technology. Design your plants, machines, or motors with Kübler. Your application is our priority: Your modifications and special solutions are implemented flexibly and quickly. We look forward to your challenge.
Applications of Kübler encoders
Various applications of industrial automation
Encoders are used wherever lengths, positions, rotational speeds, and angles need to be recorded. They convert mechanical motion into electrical signals. There are differences in the functional principles of encoders. They can thus be divided into incremental and absolute versions.We can generally supply you with all of the encoders in both shaft and hollow shaft models.
The use of hollow shaft encoders reduces costs by up to 30% and installation space by 50% compared to shaft models. This is made possible by the fact that additional couplings, mounting devices and other fixing aids are not required. To install a hollow shaft encoder, it is simply pushed onto the drive shaft, clamped and, in the simplest case, secured against rotation using a cylindrical pin. In addition, hollow shaft encoders generally require a smaller installation depth.
Application examples for encoders
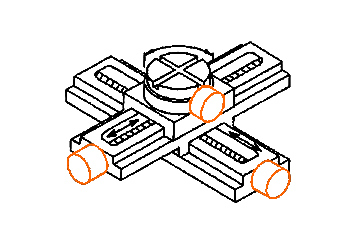
Measuring the change in the angle and rotation speed
Encoders can measure angles by the number of pulses per revolution. This is mainly used in industrial automation, whereby Kübler encoders are used in many different applications.
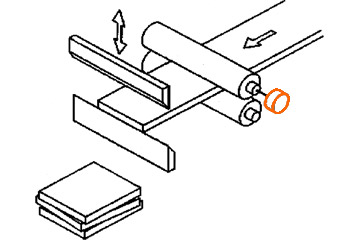
Measuring lengths and distances
Encoders provide the most accurate information when measuring lengths and distances. This is possible via the number of pulses per revolution that are counted. Rotational speeds can also be recorded with the aid of encoders.
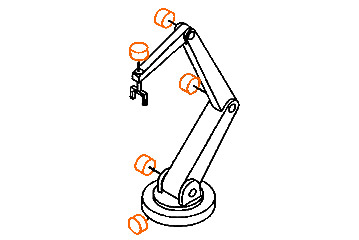
Measuring the position
In mechanical systems or hydraulic gripper arms, encoders detect the exact position in both vertical and horizontal planes.
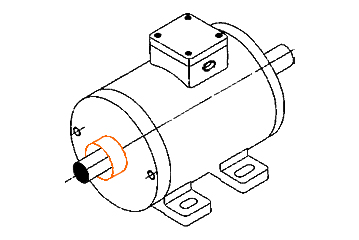
Measuring the speed and acceleration
Encoders measure the speed of motors in drive technology, for example. Acceleration can also be measured using encoders.
Kübler encoders are used in these industries
Kübler offers the right solution for any application. Sound application knowledge in many industries coupled with the highest quality awareness for products offers you the security of having a powerful and reliable partner on your side. We are also happy to take on individual challenges – your application is our priority!Functional principles of encoders
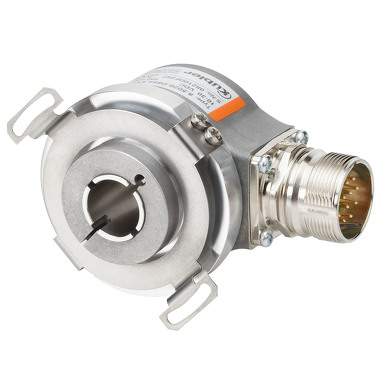
Incremental encoders for optical scanning
A rotatable disc is mounted between an LED and a receiver unit. A grating is applied to this disc. The light emitted by the LED is modulated by the screen and the grating and strikes the receiving unit, which delivers a signal proportionate to the brightness. When the disc is rotated, this signal has an approximately sinusoidal shape.
To the incremental encoders
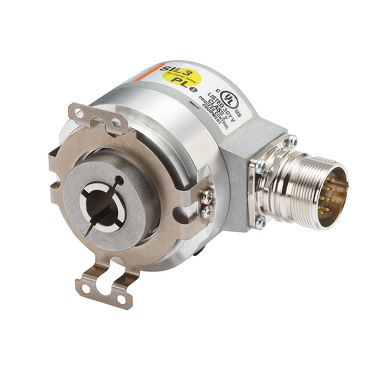
Absolute encoders with optical scanning
The light emitted by an LED is modulated by a code pattern applied to a rotating disc and scanned by a special Kübler Opto ASIC. Each position is assigned a unique bit pattern, which is usually available as a Gray Code. The advantage over incremental encoders is that, when the encoder is switched on, any motion of the shaft in a de-energized state is immediately detected and the correct position is available.
To the absolute rotary encoders
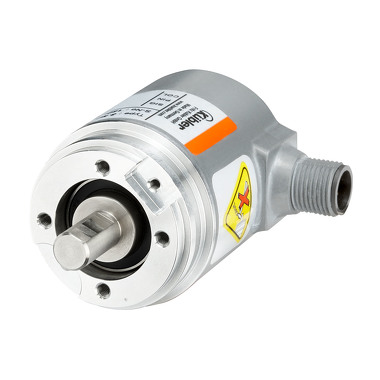
Encoders with magnetic scanning
The magnetic field generated by a rotating permanent magnet is scanned by an ASIC sensor. Each angular position is based on field vectors, which are converted into an electrical signal by the ASIC. Depending on the model, this is transmitted as an incremental signal, in absolute form as SSI, 0 to 10 V, 4 to 20 mA or as a Fieldbus signal.
To the magnetic encoders
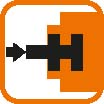
Especially robust encoders
thanks to Kübler Safety Lock™
All Kübler encoders have a special Safety Lock structure. Interlocked bearings, large bearing clearances and extra-strong outer bearings provide Kübler encoders with stabilization under vibration and robust protection against installation errors. This eliminates machine downtime and repairs.
DOWNLOADS
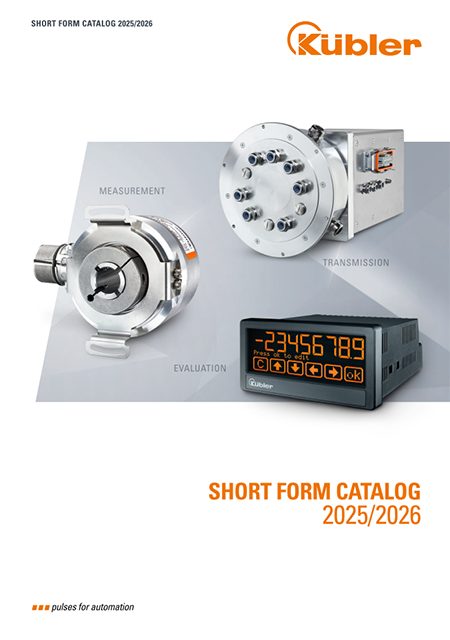
20.05.2025
∼ 15.054 MB
Short form Catalog 2025/2026
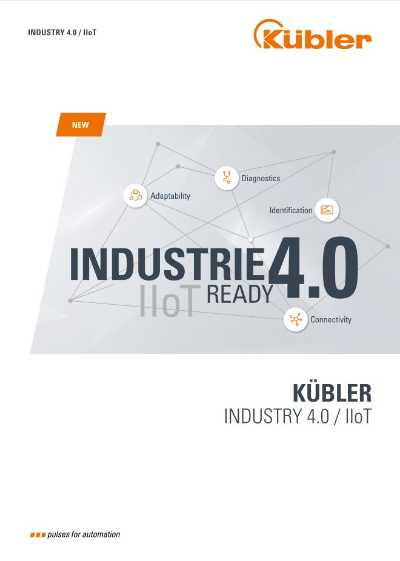
29.03.2023
∼ 2.183 MB
Industrie 4.0 / IIoT ready
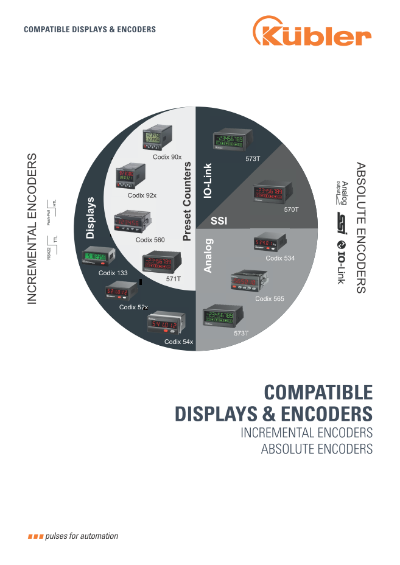
10.07.2023
Compatible displays & encoders